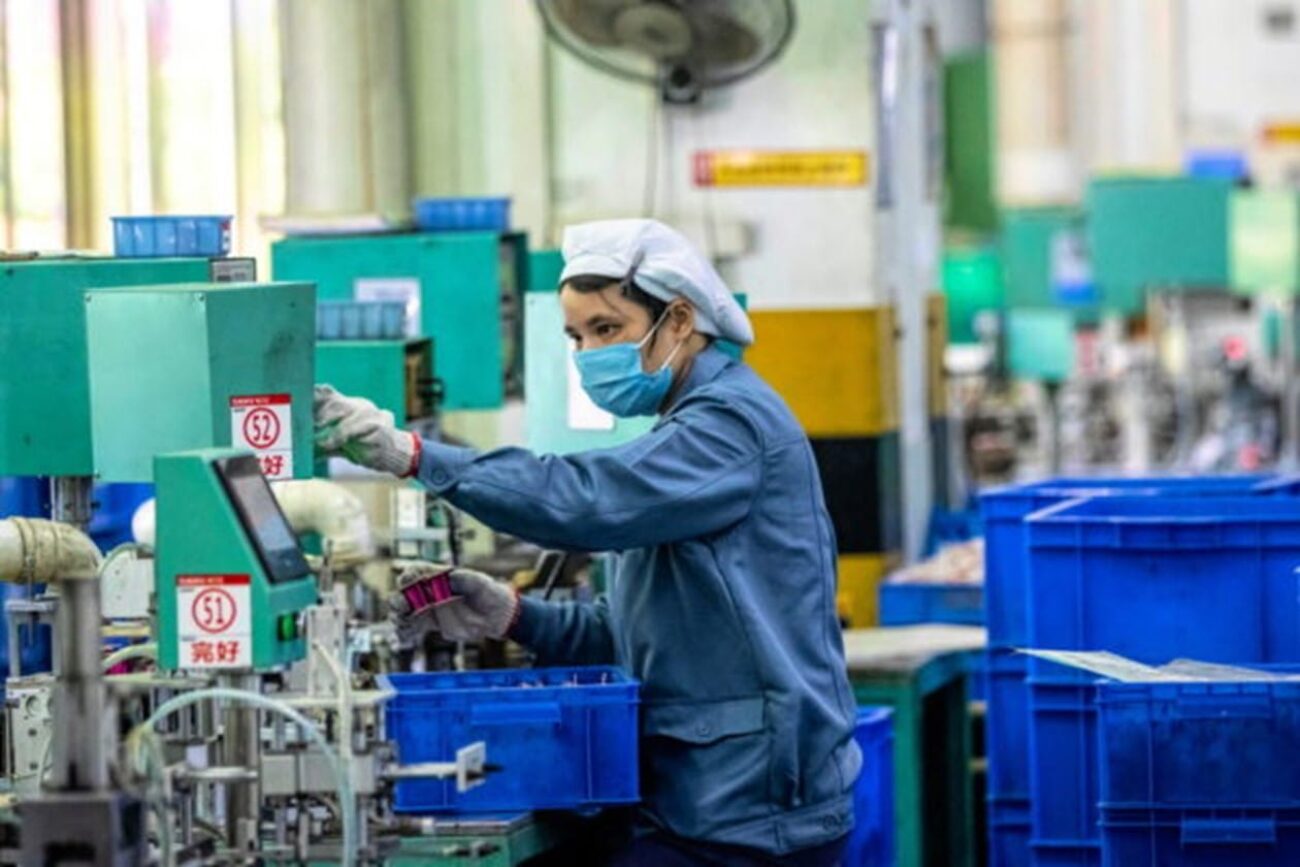
At Impactt, we believe that managing global supply chains begins with understanding the perspectives of the people who work in them. First and foremost, we place worker perspectives at the core of our work, believing that workers themselves are the best monitors of their working conditions. When looking to improve working conditions we also seek to understand the challenges and perspectives of other actors along the value chain. Be it HR teams, sustainability managers, to commercial teams, and chief executives – they all form an important piece of the stakeholder pie.
Impactt China have spent the past few months interviewing Chinese factory management teams in the electronics, printing and packaging, auto equipment and garment sectors to ask them a very simple question: how optimistic are you about the future of your business? What we heard were perspectives that point to both the economic uncertainties following months of factory shutdowns, and a shift in attitudes towards the future as China transitions out of COVID. Our conversations highlight two common themes that, through our work in China and supply chains globally, we see as having the biggest current impact on the workforce and China labour trends.
Orders: A Mixed Picture
Without the ability to forecast orders, HR managers at the factory level are unable to make informed decisions when it comes to recruitment practices. The ripple effect of this is a smaller workforce with longer, unpredictable hours and low levels of job security.
“Orders continue to fall from Europe and America and our factory is getting less busy. This has frozen our hiring and makes it difficult to predict future orders. All this means our expectations for regular operations are low.” – Purchasing Manager, Electronics factory
One factory manager told us that since re-opening in April, orders have continued to increase, with expectations that an increase of 10% will be maintained between August and December this year. Others told us the overall business this year will be about 5% higher than last year, with some factory managers commenting that their business has good development prospects for the future and is currently growing.
What does this mean for workers?
For us, it points to the nuanced and tailored approach needed to navigate working conditions in your supply chain, even within the same sector and region, to truly understand the impact of COVID-19 on orders and planning processes effect the workforce. For workers, this can lead to job insecurity, unpredictable working hours, changing migration patterns and negative effects on health and wellbeing. Impacts are being felt differently, and factory management teams that had stronger HR processes and communication channels with workers going into the pandemic have been better equipped to adapt and demonstrate resilience.
Switching production
Among the garment factory teams we spoke to, production lines had been switched temporarily to face mask production, adapting to the soaring demand for masks globally. In response to the pandemic, some factories switched not only the type of production, but also from foreign to domestic driven orders. As one HR manager explained:
“The factory has shifted some of its orders to domestic production, due to uncertainty about the epidemic in the US which previously accounted for a large proportion of orders. But the factory is optimistic about the situation at the end of the year, the factory believes the epidemic situation and orders will improve.“
Masks are considered simple products that can be manufactured by existing production lines without much retrofitting. But re-skilling your workforce to produce a completely different product requires news ways of integrating materials and manpower within a very tight schedule. Some factories made the change within just 3 days putting enormous pressure on workers to produce a new product at speed that meets mask quality standards.
What does this mean for business?
As the picture in China continues to unfold, one thing is clear. In a time when ongoing COVID-19 restrictions is leading to cancelled or postponed due diligence efforts from international companies, many labour related issues are being left undetected and unaddressed. Furthermore, the nature of labour issues has become more subtle and complex. Conducting assessments in factories requires, now more than ever, an eyes wide open approach.
Our interviews with factory managers highlight the need for a case by case approach to labour issues rather than relying on blanket trends, particularly in a market as large and regionally diverse as China. Never has it been so important to understand the challenges and mindsets of all actors in the value chain as a means of managing risk and prioritizing remedy and prevention efforts for those who need them the most.