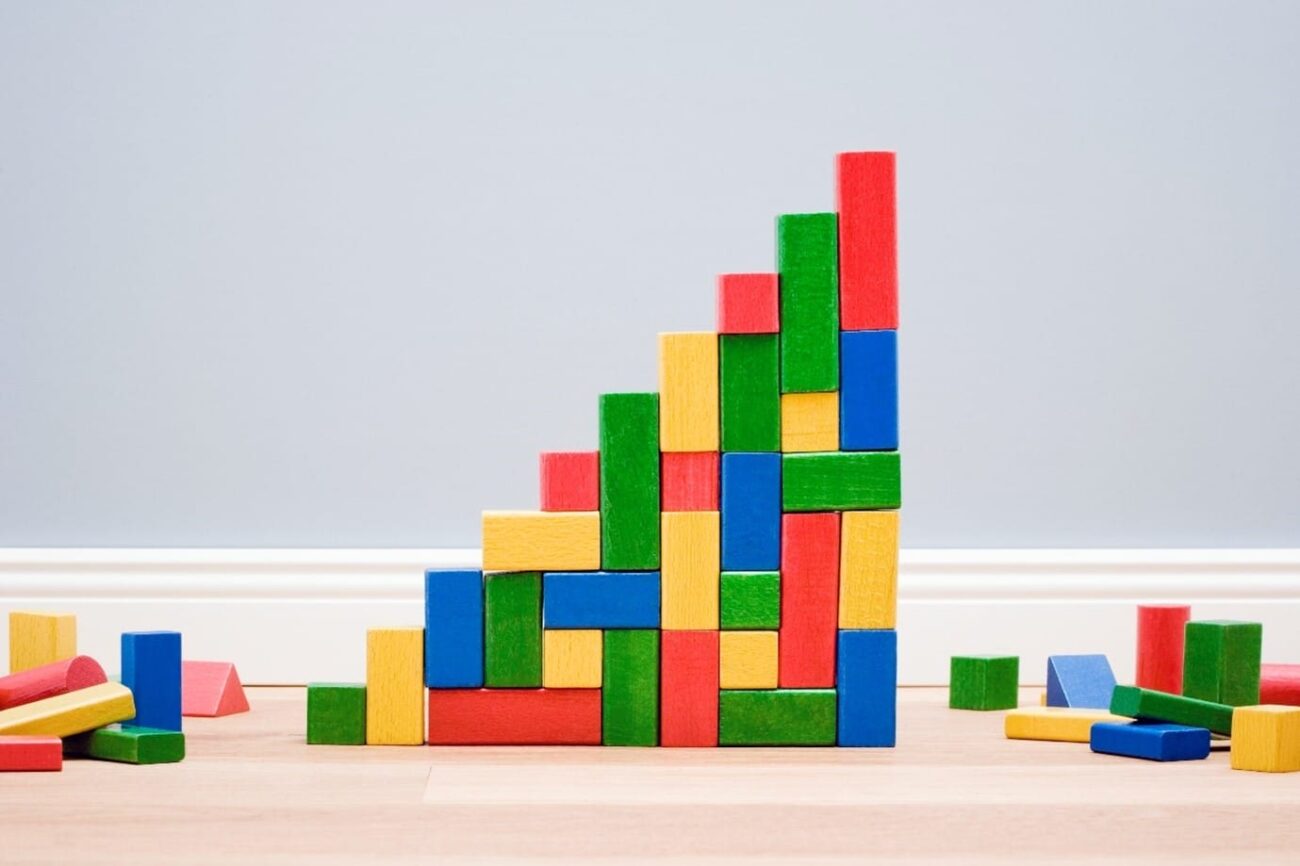
Impactt has partnered with ICTI CARE, a not-for-profit labour rights and certification organisation, to raise labour standards in Indian toy factories and help create an internationally competitive toy industry in India.
On 3 October 2016, the two organisations announced a 12-month incubator programme to accelerate progress on pressing social compliance issues in India’s toy supply chain. Impactt will manage the programme, which will provide comprehensive training and guidance for Indian toy suppliers, enabling more companies to benefit from achieving ICTI CARE certification.
So why India? What are the challenges and opportunities?
Speaking at a joint webinar, ICTI CARE’s senior responsible sourcing advisor Tom van Haaren said that with 31% of India’s 1.3bn population under the age of 14, the commercial opportunities for India’s toy industry were substantial, particularly as more people join the middle classes. Estimates are that Asia will be home to two thirds of the world’s middle classes by 2030.
With this in mind, van Haaren said that “getting products into the hands of Indian consumers will be a high priority for Indian toy manufacturers”.
The Indian toy market is currently worth approximately $1.12bn and its formal sector is growing rapidly at 12-15% annually. However, imports still dominate over home-grown businesses, particularly from China.
In order for the Indian toy industry to raise its game, it will need to navigate the risks posed by the country’s complex legal regime and address multiple labour issues.
Impactt’s founder and director, Rosey Hurst, said that gaining greater visibility over working practices of all workers would be vital. Describing a fragmented workforce comprised of permanent workers, subcontracted workers and daily casuals, all with differing rights and minimum wage levels, Hurst said the situation was one of “triple trouble”, highlighting that prominent issues included working hours and pay, health and safety and sexual harassment.
“Informal working can be useful to manage seasonal peaks, but workers don’t have the same level of protection,” she said. “We’ll be checking suppliers’ hiring practices and how they work with subcontractors and home-workers in the informal sector. It’s critical that we develop audit protocols to cover all workers, and that everyone’s rights are equally well protected.”
Despite the challenges ahead, Hurst said that there were benefits of sourcing in India compared to China. “Many companies are diversifying into the [Indian] toy sector from more high-end sectors, and Indian entrepreneurs are beginning to invest too,” she said. “India is also known for having skilled workers on the production line, particularly in apparel and toys. This could give them the edge.”
ICTI CARE in India
ICTI CARE is currently working with 14 toy factories (nine of which are certified according to its Code of Business Practices), mostly in Southern India. These factories employ some 4,750 workers, and many have re-tooled to make toys, having previously produced plastic components for carmakers and other industries.
Introducing Impactt and ICTI CARE’s 12-month incubator programme
Impactt and ICTI Care created the new incubator programme based on feedback from more than 12 brands and suppliers, following a stakeholder workshop in June 2016. Among suppliers’ key requirements were greater clarity on the ICTI CARE Code and Indian law, more robust auditing processes, and regular stakeholder communication.
Leveraging its longstanding experience of applying global knowledge to local contexts, Impactt’s on-the-ground team in India will help suppliers to interpret ICTI CARE’s Code within the context of local laws and challenges.
“We’re delighted to be working with ICTI CARE on our co-created12-month incubator programme,” said Hurst. “We aim to help participating toy factories in India get out of the blocks fast, and accelerate progress on the ground, building on ICTI CARE’s strong work in China.”
“In our experience, factories with engaged workers produce better products, which is why we say what’s good for workers is good for business,” Hurst added.
Impactt will bring its expertise to bear at both ends of the supply chain as it seeks to “deliver for all parties in India”. Senior project officer Olivia Windham Stewart will manage the programme, while Impactt’s India team will deliver the programme on the ground. The team will include its India country manager Mohammed Saleem, experienced auditor Manoj Kumar, senior ethical trade consultant Vinita Singh, and former labour lawyer and advocate, Retu Singh.
The programme has four key pillars:
1. Clarifying legal requirements
Impactt will create a simplified, user-friendly guide to the ICTI CARE Code, with a particular focus on Indian law.
2. Optimising audits
Collaborating with ICTI CARE, Impactt will optimise audits (including by supporting ICTI CARE’s current auditing partner and appointing new partners), to create a clearer, fairer auditing process. In addition, the Impactt team will provide practical guidance and recommendations to help factories to make improvements and develop a self-assessment system for suppliers.
3. Building capacity
Impactt’s comprehensive capacity building programme for ICTI factories will help suppliers to better meet ICTI CARE requirements. In particular, the team will develop and deliver tailored awareness-raising training sessions in factories, as well as group workshops.
The team will provide ongoing coaching for suppliers and help factories to capture results, share best practice, and build the business case for engaging with the ICTI CARE programme.
4. Communicating and convening
To encourage ongoing interaction and awareness-raising, Impactt will develop a 12-month stakeholder and communications programme and share monthly newsletters with participants. The team will organise quarterly workshops in Mumbai and is also exploring an online platform for suppliers to exchange knowledge and experiences.